Screen GP Australia’s Managing Director provides and update on Screen’s latest solutions and introduces our wonderful staff. Andy McCourt provides an interesting history of Screen in Australia and New Zealand. Screen GP Australia would like to thank our customers and partners for supporting us over the last 35 years!
KP LLC invests in the Truepress Jet520HD+
Truepress Jet L350UV Plus Digital Label Press at United Labels 2022
Onpack Upgrade to Truepress Jet L350UV SAI S 7 Colour
CxF Spot Colour Management Solution
Why working with spectral colour data is beneficial Conventional ICC-based colour management is effective in the standard CMYK printing world, such as the commercial printing market. However, in the packaging printing market, where spot colours are regularly used and there’s been no solution for this until now, spectral could be the answer. This article will… Read More »
Why working with spectral colour data is beneficial
Conventional ICC-based colour management is effective in the standard CMYK printing world, such as the commercial printing market. However, in the packaging printing market, where spot colours are regularly used and there’s been no solution for this until now, spectral could be the answer. This article will show why this is so, summarise the key benefits of working with CxF data, and explain how spectral CxF data can easily be used throughout the entire production process – from design to print.
Initially, it may seem cumbersome when you explain to printers that their daily business will be simplified by implementing spectral data as a cornerstone to their colour workflow environment. The concept may seem complex. Until now, the CxF open standard has been in the early stages of true adoption, and we still find some resistance to change. This fear is natural, but it can also enable companies to be more profitable when they embrace new technology advancements.
The colour exchange format (CxF), which is the basis for spectral colour data, is discussed in many expert industry forums related to colour management. This is for good reason, and it’s already referred to as ‘the silver bullet to communicate and manage colour’.
Let’s explain why and introduce you to some new features which make working with spectral data simple and help boost the overall efficiency of your business.
Advantages and potential of spectral data
A huge advantage of capturing CxF colour data is that all characteristics of the colour are included and easily communicated. This sounds simple, right? But if you take a good look at the daily business of many companies, you will see that many members of the graphic arts industry are struggling with challenges around a lack of complete or insufficient colour data. They usually receive this data from their clients or may provide it to their suppliers.
To communicate colour effectively, it is not enough to describe the solid tone value as is done in most cases today. You need to include all the aspects of a colour, such as the halftones, and even the overprinting behaviour. Ultimately, this is crucial information as spot colours are used not only for solid brand colours but also separation colours. This includes halftones and gradations. Moreover, these separation colours may be overprinted with each other.
This is of great importance for packaging, to secure brand identity and colour consistency. With spectral data and suitable tools, you can easily do this.
Why spectral?
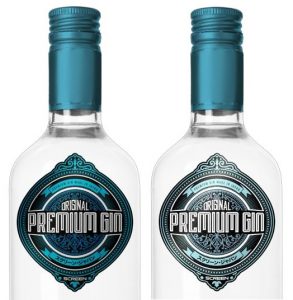
Brand colours, often expressed as Pantone colour names, are generally specified using CIE Lab values. The Lab value describes how the spot colour looks under certain lighting conditions (D50). It does not describe how the midtones should behave nor provide any information about what the colour looks like under other lighting conditions. This lack of lighting information may cause metamerism, a phenomenon where colours look different when light source changes.
To maintain global colour consistency, brands are using CxF/X-4 (colour data exchange format part 4, registered as ISO 17972-4:2015) to communicate colours. CxF/X-4 allows colours to be communicated using spectral data, including midtones and ink opacity information. This additional data is used to calculate colour differences under various lighting conditions, not only on the solids but also the midtones and overprints (or mixture of multiple colours).
Analogue to Digital
Today, CxF is mainly used in conventional (or analogue) production printing. Printers use the CxF data to blend inks and verify colour differences in optical wavelength.
Some products (print jobs) originally designed for analogue printing production are sent to digital printing. This may occur as a repeat production in a smaller run, and versioning for different variations, etc.
When these jobs are sent to digital printing production sites, print operators may face difficulties matching colours against print samples from an analogue press. If the design contains midtones or spot colour overprints, it may be nearly impossible for the operator to adjust print settings (such as tone curves or colour correction table) to get an optimal result.
However, if the print job is sent as a CxF embedded in a PDF to a CxF-aware DFE (such as SCREEN’s EQUIOS), the print operator should deliver an optimal result from the first output without needing cultivated operator skills.
This, of course, does not mean that the digital press will increase its colour gamut by using CxF. For the digital press to achieve equivalent result to the analogue press, the design must use colours within the digital press’s colour space. The DFE will find the best colour combination using the fixed colour sets used by the digital press to express spot colours defined by CxF.
Working with CxF data is simple
There are still many reservations in the market around the adoption of CxF data. In our experience, this is often related to the uncertainty of how to manage CxF data, the benefits, and how to go about implementing a CxF-based workflow. People are often under the impression they will need a lot of time to create the initial CxF data, which is necessary to get started. In some cases, they are right. In the commonly used, conventional way, it is time-consuming, as you need to create, print and measure CxF tint ramps for all the individual colours you need to work with.
CGS ORIS & SCREEN
CXF TOOLBOX technology is a user-friendly solution developed to minimise the burden and maximise the benefits and advantages of working with CxF. To combine the original CGS ORIS technology and SCREEN’s unique EQUIOS technology, SCREEN simplifies the user’s operation even more, and offers the turnkey solution for the Truepress Jet L350UV SAI.
Embedding CxF to PDF
EQUIOS DFE with the CxF option includes a licence for CXF TOOLBOX and CXF CLOUD from CGS ORIS. CXF TOOLBOX is used to create and embed CxF data to PDF. CXF CLOUD is an online database to share CxF data among multiple sites.
Creating CxF
To create a CxF data for a spot colour, a special chart must be printed on the target analogue press using standard printing process.
The chart consists of tint ramp over white and 100% pre-printed black for opacity calculation.
By measuring and evaluating the 100% solid patch’s spectral data with CXF TOOLBOX, printers will be able to adjust the spot colour ink at ink dispensing system.
Once the solid is certified, measure the other patches in the tint ramps and fill in the CxF/X-4 metadata fields (colour name, substrate, etc.) before saving or uploading to the CXF CLOUD.
These steps must be repeated for all colours on all printing processes (target device and substrate).
Creating CxF, the easy way
Printing and measuring the 22 tint ramps for every colour on every print process can be expensive and time-consuming.
CXF TOOLBOX comes with a new feature to simplify these tasks. SCREEN and CGS ORIS have jointly developed this technology that predicts halftones from limited colorimetric data. It uses a proprietary algorithm and automatically generates complete CxF data.
If you select the appropriate and stable printing process, the prediction should provide a reliable result.
Fetching CxF from the Cloud
If the CxF data is ready and has been loaded to the CXF CLOUD database, you can download the data and skip the cumbersome tasks needed to prepare the CxF to be embedded to the PDF.
Via the CXF CLOUD platform, brand customers and printers can create the same colour result environment among multiple sites. It guarantees access to complete colour data – always up-to-date and available for authorised users at any time and any place in the world.
Embedding CxF to PDF
Once the CxF data for a specific job is ready, it can be embedded to a PDF. To achieve a good colour match against overprint, you should specify the ink laydown order used by an analogue printing process.
Reproducing Brand Colours with EQUIOS
EQUIOS will process a PDF with CxF embedded using the spectral data for solids and midtones, as well as opacity and ink laydown information provided in the previous step. It will calculate a best colour match for the SCREEN’s digital inkjet press, the Truepress Jet L350UV SAI.
Summary
Working with CxF data and the newly developed prediction feature makes it easy to enter the beneficial world of spectral data. It offers much greater accuracy and security (as colours are captured with all their properties and behaviour), and helps production work become simpler and faster.
The experience of one large brand customer, for example, shows a saving of a month per year in the product innovation cycle. This, of course, leads to huge cost reductions.
Spectral data helps reduce errors (during the production process and between project partners). It ensures colour data is always up to date, and provides a timeless, durable and reliable benchmark, which does not shift over time like colour cards/chips. It offers several solutions to challenges, and helps to dissociate processes from individual colour experts within a company.
Because CxF is an open standard and can be applied to each printing process and varying substrates, it also ensures a high level of flexibility. This allows for a significant simplification of the entire colour workflow, translating into greater productivity and efficiency. This has positive knock-on effects for everyone in the production process, from design all the way through to end print production.
Working with spectral data and suitable tools guarantees consistent colour all over the world, wherever and whenever colour is printed. It removes the remaining challenge in the transition from analogue to digital printing. It also expands the opportunity for users to enjoy the latest ink jet technology in the growing demand for short-run and versioning/personalisation.
New Truepress Jet L350UV SAI Movie
Extraordinary Speed And Quality Meets Unrivaled Flexibility. “SAI” refers to its extremely Stable operation, highly Accurate color reproduction, and time-tested Integrated technologies.
Truepress Jet L350UV SAI
Extraordinary Speed And Quality Meets Unrivaled Flexibility. “SAI” refers to its extremely Stable operation, highly Accurate color reproduction, and time-tested Integrated technologies.
Screen Truepress Jet 520HD at Silhouet
A great example of how our Truepress Jet520HD helped revolutionise one man’s business process! Screen has great admiration for this user who built his business around our product. Thanks to its unparalleled automation and reliability he can run his machine night and day, without affecting his ability to live life to the full!
Hubert&Co – Highspeed inkjet in-line from roll to finished book block
Hubert & Co is an end-to-end book maker with a passion for detail. Hubert & Co produces short run book jobs Inline from roll to book block on standard offset coated paper. They are able to use the same paper that they use in offset production without the requirement to pretreat or post-coat. Hubert &… Read More »